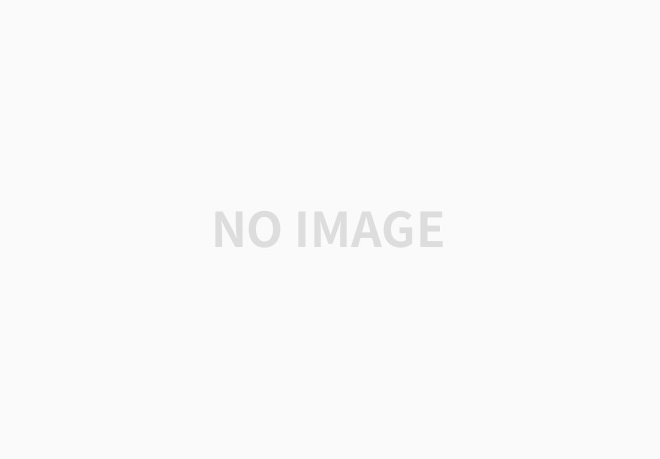
안녕하세요. 토탈 3D 솔루션 전문 기업
휴스템(Hustem)입니다.
이번 활용 사례는 레이저 3D스캐너 ZEISS T-SCAN을
BMW 공장에 적용한 사례를 소개해드리겠습니다.
뮌헨의 BMW, ZEISS T-SCAN으로
전방 및 후방 어셈블리 공정의 신뢰성 향상
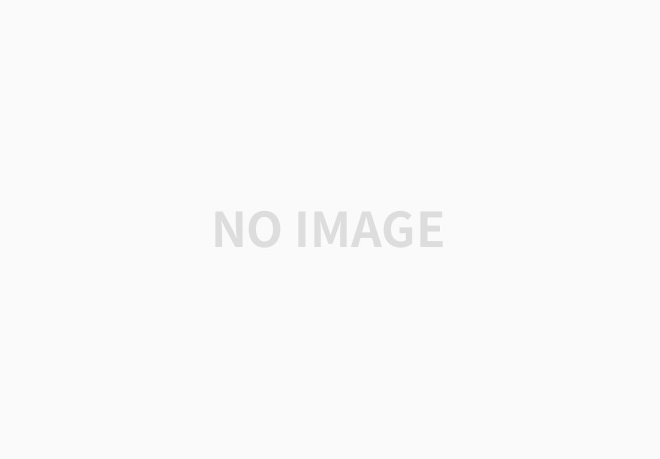
개요
매일 1,000대의 차량이 BMW 그룹 뮌헨 공장의 조립 라인에서 굴러가고 있습니다. 바이에른 주에서는 BMW 3 및 BMW 4 시리즈 모델만 생산됩니다. 여기에는 BMW 3 Touring, BMW 4 Coupe 및 M4 Coupe 모델이 포함되어 있으며, 이곳에서 조립된 후 전 세계로 수출됩니다.
프런트 엔드는 차량의 실루엣을 결정적으로 특징짓습니다. 이러한 이유로 완벽한 조립과 공동 계획을 엄격히 준수하는 것이 BMW에게 매우 중요합니다. 오랜 시간 동안 갭(gap)은 갭 게이지에서만 테스트되었습니다. 이 과정에서 허용 오차의 편차가 효과적으로 시각화되지만 오류 원인을 파악하는 데는 기여하지 않습니다. 과거에는 이러한 오류를 추적하기 위해 눈에 띄는 조인트와 갭 프로파일을 가진 차량을 측정실로 가져가서 측정을 해야 했습니다. 그래서 부서에서는 조립 과정을 최적화하기 위해 디지털화 시스템을 검색했습니다. 최종 조립 직후에 사용해야 하며 측정실에서 시스템이 수행한 것과 같은 정확한 결과를 제공해야 합니다.
솔루션
핸드헬드 레이저 3D스캐너 ZEISS T-SCAN은 빠르고 직관적이며 고정밀도로 3D스캐닝이 가능합니다. 핸드 스캐너, 추적 카메라 및 터치 프로브는 완벽하게 연동됩니다. 따라서 모듈식 시스템은 수많은 애플리케이션에 사용될 수 있고, 고유의 스캐닝 속도와 정확한 측정 결과가 큰 가치를 지닙니다. T-SCAN은 초당 21만 포인트의 데이터를 취득할 정도로 빠르게 표면 접촉 없이 3D스캐닝합니다. 추적 카메라가 스캐너의 위치를 감지하면 3D 표면 데이터는 삼각 측량의 도움을 받아 계산될 수 있습니다.
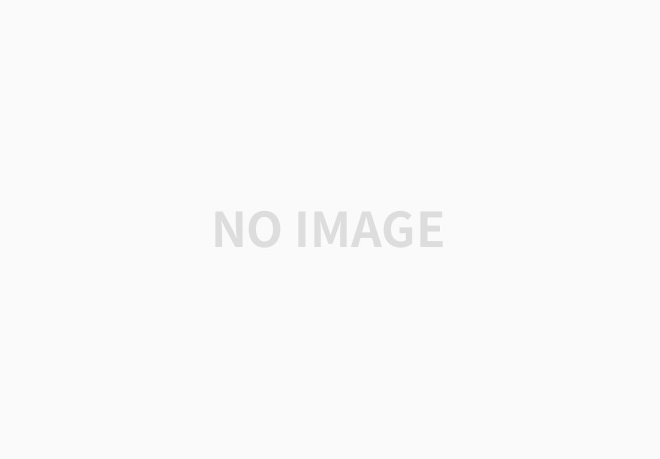
구멍 자리 또는 함몰을 포착하기 위해 ZEISS T-SCAN으로 캡처한 데이터는 실제 상태를 정확하게 설명합니다. 이를 CAD 모델에 정의된 대로 목표 사양과 쉽게 비교할 수 있습니다. 편차는 전체 표면의 잘못된 색상 비교로 사용자 친화적인 방식으로 신속하게 감지할 수 있습니다.
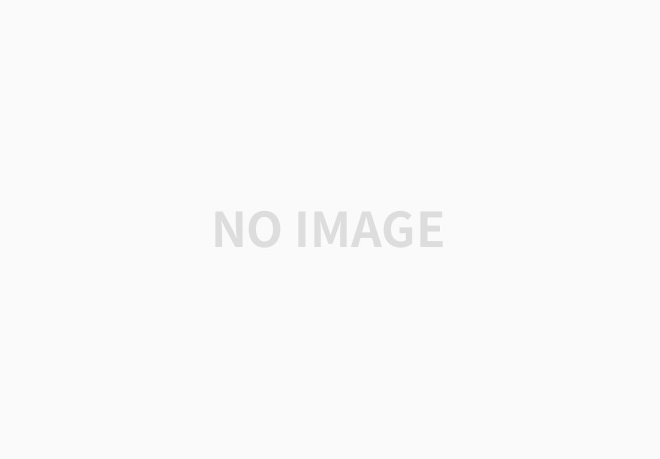
ZEISS T-SCAN은 인체 공학적인 요구 사항을 충족하므로 더 큰 부품도 피로가 없는 스캐닝이 가능합니다. 가볍고 콤팩트한 스캐너 하우징 덕분에 ZEISS 시스템은 접근하기 어려운 영역에서도 쉽게 데이터를 캡처할 수 있습니다. 직관적이고 쉬운 조작으로 응용 프로그램이나 사용자 그룹의 범위가 확장됩니다.
결과
2016년 3월부터 3명의 조립공이 하루 평균 6대의 완성된 차의 전후방을 검사했습니다. 이로써 두 부분으로 된 둥근 방열기 그릴과 이른바 BMW 신장, 전조등 및 범퍼의 조인트와 틈새 폭이 측정됩니다. ZEISS T-SCAN의 숙련된 운영자는 프런트 엔드에서 80~90 측정 지점을 캡처하고, 다양한 모델의 리어 엔드에서 40 측정 지점을 캡처합니다. 측정된 실제 값은 CAD 모델의 설정값과 비교됩니다. 2시간 이내에 전방 및 후방 끝단에 결함이 있는지를 확인할 수 있습니다. 이러한 방식으로 조립 및 자체 제작의 품질 엔지니어는 훨씬 신속하게 대응할 수 있습니다.
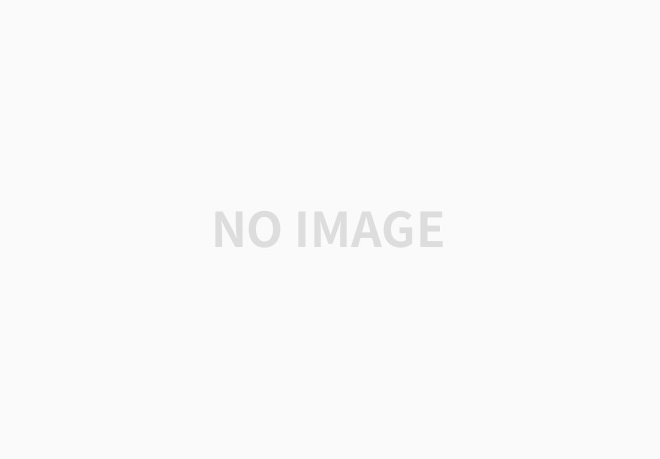
ZEISS 시스템은 품질 및 프로세스 엔지니어에게 공급 업체의 프로세스뿐만 아니라 사내 프로세스를 보다 효과적으로 제어하기 위한 중요한 전제 조건입니다. ZEISS T-SCAN 시스템의 이식성 덕분에 프런트 엔드와 리어 엔드 조립 장치를 생산 현장에서 직접 측정할 수 있습니다.
- 정확한 측정 결과로 빠른 오류 탐지
- 작업자가 쉽게 조작 가능
- 시스템의 이식성이 생산 홀에서 장치를 검사하여 오류 방지를 지원
문의전화 : 02-6262-1027
'3D 스캐너 > 레이저 스캐너' 카테고리의 다른 글
트래커형 레이저 3D스캐너 ZEISS T-SCAN 품질검사 활용 사례 [해외 사례] (0) | 2019.11.18 |
---|---|
레이저 3D스캐너 FreeScan X로 3D스캐닝하여 품질검사까지! [해외 사례] (0) | 2019.11.18 |
열차 편차 검사에 레이저 3D스캐너를 적용한 사례[FreeScan X, 해외 사례] (0) | 2019.11.18 |
레이저 3D스캐너 FreeScan X7으로 대형 가스 터빈 검사 [해외 사례] (0) | 2019.11.18 |
레이저 3D스캐너 ZEISS T-SCAN으로 검사 프로세스 시간 단축 [해외 사례] (0) | 2019.11.18 |